Supply Chain Management
The management of suppliers and partners, an elementary part of the supply chain, is an important pillar of corporate responsibility regarding environmental, social and governance dimensions.
Copel’s suppliers vary according to the business and include power generators and transmitters, manufacturers of materials, heavy machinery, service providers, among others.
Through strategies and contractual requirements, Copel improves the management of its production chain and optimizes resources for the benefit of the community, so as to incorporate into internal and external relationships values that enhance citizenship, dialogue between the parties, ethics and transparency.
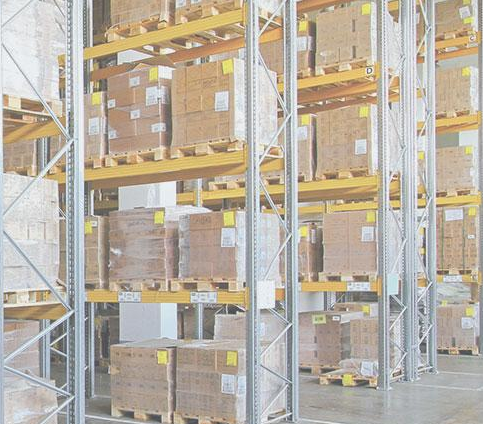
Copel’s Integrity Program provides for the sending and evaluation of an Integrity Questionnaire to individuals or legal entities that have or intend to have a business relationship with Copel, among other transactions, in the formation of partnerships or hiring of suppliers for new business, with the purpose of classifying the degree of risk of each supplier or partner, as per the provisions of NPC 0201 – Procurement Policy.
Internally, the matter is governed by corporate standards and policies that deal with contract management, supplier evaluation, contracting procedures, Code of Conduct, Procurement Policy, privacy rules and personal data protection, among others.
In addition to strategic financial and operational objectives, Copel’s contractual demands seek to incorporate the Principles of the Global Compact, among other sustainability benchmarks, into its supply chain.
The Company’s suppliers must follow the provisions of the Code of Conduct and Copel’s Supplier Manual, with the possibility of applying sanctions in the event of any violation of these provisions.
Copel’s Code of Conduct and Supplier Manual establish the conduct guidelines to be observed by suppliers in business and operational relationships with Copel, which include the following topics: forced and child labor; work conditions; health and safety; discrimination and harassment; freedom of association and collective bargaining; greenhouse gas emissions and energy consumption; pollution prevention and waste management; resource efficiency; biodiversity, deforestation or land conservation; anti-corruption and conflicts of interest; and anticompetitiveness.
The Vice-Presidency of Finance and Investor Relations (VPFI), through the Supply Office, is responsible for defining policies, guidelines and standards on processes related to supplier management, including environmental, social and governance aspects, which are applied by the business areas.
Purchasing practices in relation to Copel’s suppliers are continually reviewed to ensure alignment with the Code of Conduct and to avoid possible conflicts with ESG requirements. Periodic review of documents includes draft contracts (services and materials), the Code of Conduct, the Supplier Manual and Critical Supplier Identification Methodologies.
Review work is carried out by multidisciplinary teams from various departments (management, legal, compliance, business areas), which are formalized in specific working groups.
Copel’s supply chain management strategy is guided by Copel’s Internal Regulations and Strategic Planning.
The strategic objectives are translated into procedures and management practices, linked to three macro processes:
- Selection and Qualification of Suppliers;
- Development and Relationship with Suppliers; and
- Evaluation and Monitoring of Suppliers.
Additionally, Supplier Management is carried out in line with the corporate strategies defined and approved by the Board of Directors – CAD. Among the CAD Guidelines directly related to the issue of suppliers, the following stand out:
- Have discipline in capital allocation and technical rigor in asset management, planning and project execution;
- Achieve efficiency standards of the best companies in the sector, promoting innovation, investment in technology and optimization of the workforce;
- Consolidate the culture of safety, health and quality of life.
This alignment even extends to the best practices in the market and acting with socio-environmental responsibility and with a strong focus on sustainability.
Training for Buyers or Stakeholders:
Copel periodically conducts training for buyers and other parties involved in the contract, on issues related to ESG aspects. Training is provided on the legal aspects of the hiring process and on socio-environmental aspects. For example, in 2022 and 2023 training was carried out on Human Rights Due Diligence, a practice that is being implemented in all of the Company’s activities, in accordance with NAC 030373 Human Rights – Protection and Diligence. In 2024, Copel promoted initiatives for its internal public, such as the Sustainability Course and the ESG Integrated Week.
Integrity and Compliance:
Copel’s Integrity Program provides for the sending and evaluation of an Integrity Questionnaire to individuals or legal entities that have or intend to maintain a commercial relationship with Copel in the following transactions:
- Forming partnerships or contracting suppliers for new business, in accordance with the provisions of NPC 0201 – Procurement Policy;
- Sponsorships pursuant to provisions of NPC 0309 – Sponsorship Policy;
- Agreement, in accordance with the provisions of NAC 030906 – Agreement Management; and
- Mergers, acquisitions or divestments.
Based on the evaluation of the supplier’s or partner’s responses, the Company’s Compliance area classifies the degree of integrity risk and informs the Company’s area interested in contracting about actions and/or recommendations of the partner’s risks.
Exclusion of suppliers from the contracting process:
Phase 1 – Supplier pre-selection:
During the contracting process, after consulting prices with potential suppliers, Copel requires that proof of minimum qualifications related to ESG be presented, such as legal, tax and labor, economic-financial and technical compliance.
In technical qualification, the requirements are specific for each type of material or service to be contracted. For products or services that have an environmental or social impact, certifications or attestations from the competent bodies are required, which prove the conformity of the product or service with the required socio-environmental parameters. In addition, certificates of technical capacity, issued by other companies, are required, which attest to the experience and quality of the services or products covered by the contract.
Phase 2 – Supplier selection:
During the ESG qualification phase and, before formalizing the selected supplier, all contracts included in formal medium and large value modalities undergo an integrity assessment (background check), which is in-depth in exceptional contracts (contracting modality to be adopted in cases where price consultation or market dispute is unfeasible or inconvenient) and/or large amount, and the deadline for suppliers to demonstrate the minimum ESG requirements is until the completion of this phase.
If the company does not meet the integrity requirements or does not have any of the items required in the qualification documents related to ESG, a note is made in the process in the form of a negative recommendation for hiring.
Social and environmental risks, included in the operational risk category, are those related to the impacts of Copel’s operations on society and the environment, which may generate regulatory and financial liabilities and affect the Company’s reputation. This risk is also related to environmental and social impacts on Copel’s operations, such as the effects of severe weather, dam rupture, scarcity of natural resources, mobilization of communities or health crises, which may affect the performance of operations and services provided, causing losses to Copel.
In compliance with the legislation, and in order to guide and establish responsibilities for the areas responsible in the Company and for suppliers, in all hiring, it is evaluated the need to prepare a matrix of risks and responsibilities, which considers, in addition to strategic aspects related to the purpose of the hiring, aspects of social and environmental responsibility, provided for in the Sustainability Policy and other corporate policies of Copel.
The results obtained with the application of the Risks and Responsibilities Matrix serve as guidance for the identification of the major points of attention in the execution of the contract and the severity of their materialization.
Among the risks related to the supply chain, the following stand out: accidents involving employees; accidents or damage to the population; socio-environmental compliance; integrity (corruption and bribery); precarious facilities and working conditions.
Especially in the economic-social dimension, there are risks related to Copel’s economic-financial dependence, legal obligations, tax, social and labor charges, and salaries and additional payments.
The risks related to the environment involve non-compliance with environmental legislation, inadequate origin of inputs and deficiency in waste treatment. Copel seeks to mitigate these risks by determining strict contracting rules, therefore, only suppliers with the best ESG performance will be chosen when selecting suppliers and awarding contracts, reaffirming the commitment to sustainable development.
In order to direct management actions with its suppliers more efficiently, Copel identifies those whose inputs or services are considered critical for the Company.
“Critical suppliers” are considered those whose supplies made to Copel pose a significant risk to the Company, from the perspective of a possible disruption of supply, as well as those with greater risk in economic, environmental, social and governance aspects.
Suppliers are evaluated according to the degree of risk of disruption and the degree of impact on Copel, considering legal, financial, environmental, occupational health and safety, population safety, image, customer and customer perception aspects. society, and processes. Those whose risk is considered significant are classified as critical suppliers.
Due to the high number of suppliers and considering the peculiarities of contracting each object, Copel established criteria for identifying and classifying critical supplies, in order to define management metrics that guarantee the availability of goods or services classified as such. The criteria for identifying and classifying critical suppliers take into account at least one of the criticality conditions listed below: market availability, economic and financial dimension (value), social dimension and environmental dimension.
The definition of appropriate strategies for each of the criticality criteria allows for the development and evolution of supplier management and, consequently, of its supply chain.
Critical Supplier Identification Methodology:
The methodology lists the products and services by object whose discontinuity of supply represents risks of significant impact on the development of its operational and business activities, and the evaluation criteria vary according to the specificity of each business (distribution, generation and transmission of electric energy).
For the identification of critical suppliers in ESG criteria, we have the following premises:
- Environmental: an analysis is carried out of all types of contracts carried out by the Company, in order to list those products and services that have the greatest impact related to the emission of greenhouse gases.
- Social: an analysis is carried out of all types of contracts carried out by the Company, in order to list those products and services that have the greatest impact related to working conditions.
- Governance: an annual survey is carried out with all suppliers with active contracts with the Company, in order to identify and assess integrity risks in commercial relationships with third parties.
After identifying the critical products and services for the Company, risk mitigation actions are carried out through the creation of contractual provisions (clauses on specific requirements and inspections).
Critical Supplier Identification Table | Values for 2022 | Values for 2023 | Values for 2024 |
Evaluated Direct Suppliers | 8,069 | 8,787 | 7,373 |
Identified Critical Suppliers | 142 | 187 | 188 |
Spending with Critical Suppliers in relation to the total | 11.91% | 6.25% | 3.50% |
Copel evaluates its suppliers in relation to contractual obligations. The documentary inspection is carried out by the Documental Inspector, who is an employee formally designated to assist the Contract Manager in monitoring, controlling and inspecting the obligations related to the documents required in the contract.
The contracts signed by Copel with its suppliers require the presentation of certificates and other documents that at least prove the contracted company’s tax compliance. In addition, depending on the specificity of the contracted product or service, it is required to present specific certificates and documents, of a social, labor, and environmental nature, such as, for example, when contracting services with assignment of outsourced labor, the monthly proof of payment for outsourced employees, as well as, when contracting a waste disposal service, presentation of the official disposal certificate is required (in accordance with local legislation).
Copel uses a digital platform for posting documents by contractors, with the aim of controlling, monitoring and auditing the documents presented, referring to labor, social security, land, safety and occupational medicine obligations.
The supervision of the provision of services or delivery of products is carried out by the Operational Inspector, who is an employee formally designated to assist the Contract Manager in monitoring and inspecting the physical execution of the object of the contract (provision of services, execution of works, contractual milestones , quantity and quality of equipment/materials used, etc). The inspection terms are described in the contracts according to the specific needs of each contracted object.
Document inspections and inspections in the workplace serve as a subsidy for evaluating suppliers, called the Supplier Performance Index (IDF), whose assumptions are determined by each business, aiming to contemplate the most appropriate evaluation criteria for each.
In the case of Copel Distribuição, the criteria of quality, punctuality, compliance, work safety, production of service units, sustainable management, supplier registrations, and degree of relationship are evaluated.
In the case of Copel Geração e Transmissão, health and safety criteria are evaluated (quality of Personal Protective Equipment – PPE; quality of delivery and unloading equipment; quality of tools and equipment used; quality of uniforms and presentation of professionals; and organization of the work environment), competence and commitment (training and commitment of the workforce; quality of service supervision (agent); rework; time management; relationship quality; and quality of inputs and materials employed), and customer service requirements (knowledge of the contract; invoice; documentation; and packaging and labeling).
Based on the results of the Supplier Performance Index (IDF), Copel promotes the development of its suppliers. Deficiencies common to all suppliers are identified, which serve as a basis for carrying out specific workshops and training. For suppliers with low performance in any item, feedback is provided with a recommendation for improvement for the remainder of the contract execution. In addition, Copel’s contracts have an administrative sanctions clause, which provides for the application of formal warnings for non-compliance with contractual provisions. In the event of repeated non-compliance, or in the event of non-compliance with clauses considered serious, the sanctions are staggered with financial fines, which may, in extreme cases, lead to contractual termination.
Table of the Supplier Evaluation Program – Supplier Performance Index (IDF) | Values for 2022 | Values for 2023 | Values for 2024 |
Evaluated Suppliers | 422 | 312 | 451 |
Percentage of Critical Suppliers | 14.79% | 49.73% | 49.47% |
Suppliers with Negative Impacts | 70 | 93 | 104 |
Suppliers with Action Plan for Improvement | 0* | 0* | 0* |
Suppliers with Terminated Contracts | 3 | 4 | 2 |
*No suppliers were identified in need of implementing action plans for improvement.
Copel’s business partners are informed about the anti-corruption measures adopted by the company, as well as its policies and standards, through the Supplier Manual. This document is made available when proposals are requested or when the contract is signed, accompanied by a Statement of Knowledge and Commitment.
Supplier Development
The transfer of knowledge, technologies, safety practices, management and socio-environmental responsibility aims to build and maintain an increasingly capable and sustainable supply chain.


Supplier Management at Copel Generation and Transmission
At Copel Geração e Transmissão, Supplier Management contributes to sustainable development by improving the management of the production chain and optimizing resources for the benefit of the community.
Aligned with the best management practices, the Certification Program and the Supplier Development Program at Copel GeT seek to promote recognition and help suppliers improve their performance in the environmental, social and economic dimensions.
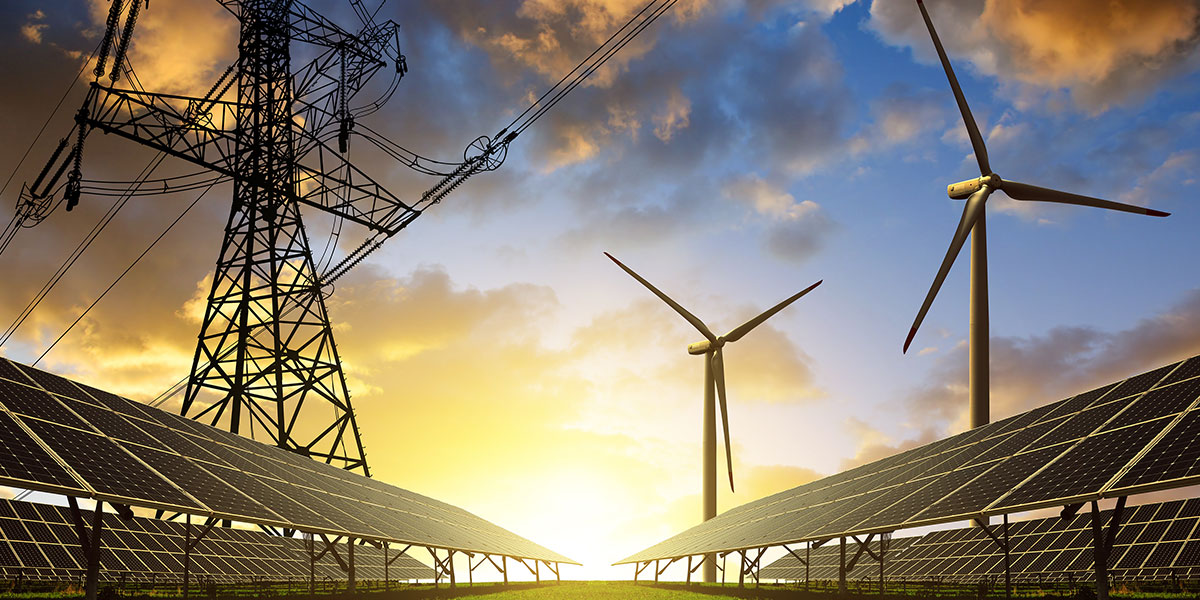
Supplier Management at Copel Distribuição
For Copel Distribuição, suppliers are strategic partners, since they are suppliers of inputs (materials, equipment and services) that are indispensable for the Company’s business.
Copel Distribuição uses as main criteria in contracting suppliers, compliance with labor legislation, respect for human rights, fiscal integrity and environmental responsibility. The criteria are defined in the bidding notices, contractual clauses, supplier registration manuals, code of conduct, in addition to standards and technical manuals permanently available to interested parties on the organization’s website.
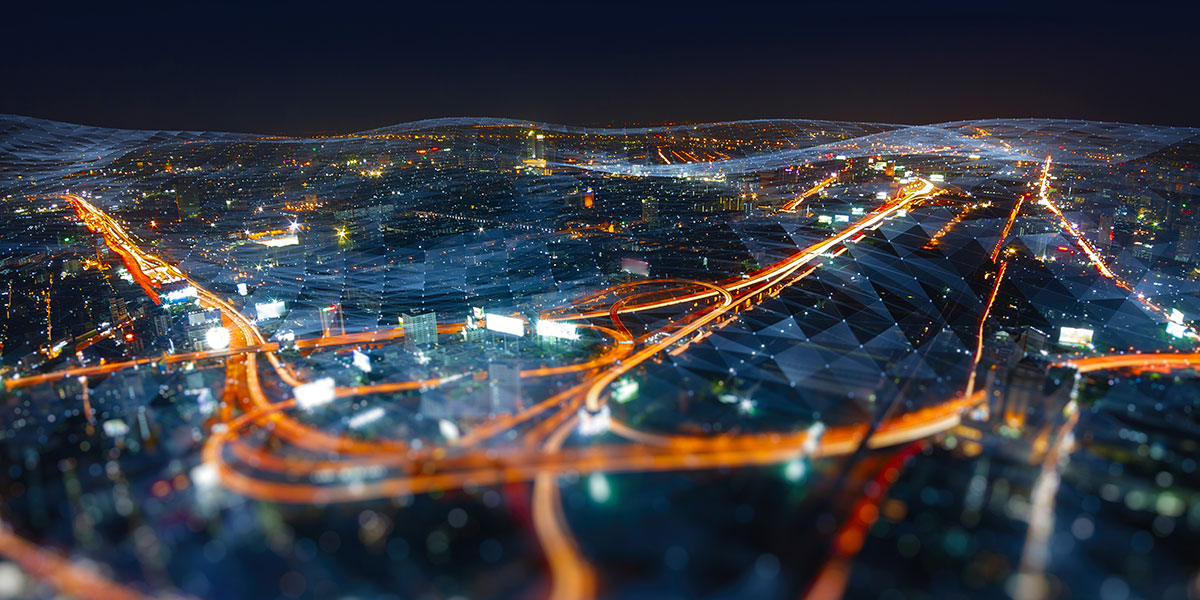