Occupational Health and Safety
At Copel, people’s health and safety is a fundamental factor of success and organizational longevity and, for this reason, it is contemplated by the top leadership as a Company strategy, having as its main performance goal of caring for people’s health, safety and quality of life the severity rate of accidents involving employees and contractors. This goal is unfolded and monitored in the management commitment of all areas of the Company.
The Occupational Health and Safety Policy supports and guides the construction of a healthy and safe work environment for everyone. It aims to maintain and improve the preventive systemic approach in order to eliminate dangers and reduce risks, with the objective of preventing accidents and ensuring safe and healthy working conditions, and protecting the human rights of employees and contractors.
This process allows employees and managers to participate and be agents in the construction of actions for continuous improvement in the protection and promotion of safety, health, and well-being for all.
In this way, all employees and managers develop, together with their regular activities, a routine of care with safety, so as to ensure that no service is performed outside of Copel’s existing procedures. This is reflected in the continuous improvement of programs and processes related to the theme.
In a corporate manner, policies, norms, instructions and programs that apply to the entire Company are implemented. The wholly-owned subsidiaries that make up the group, for having different characteristics of activities, develop programs and actions directed to their business.
The care with the theme is coordinated by employees of the company’s own staff, with professionals from the Specialized Services in Safety Engineering and Occupational Medicine (SESMT). It is noteworthy that, the Management System in Health and Safety is composed of a series of documents of policies, norms, procedures and programs that observe the best market practices, as well as the applicable standards and norms, supported by the legislation Ordinance 3.214 of June 8, 1978 and Federal Law No. 6.514 of December 22, 1977. Its main elements are:
- Occupational Health and Safety Policy
- Risk Management Program – PGR
- Occupational Health Medical Control Program – PCMSO
- Internal Accident and Harassment Prevention Committee – CIPA
- Health and Safety norms and instructions
- Occupational Medicine Norms and Instructions
It is worth noting that 100% of our own and outsourced employees are covered by an occupational safety management system.
Safety inspections and checks are carried out periodically to reduce the risk of accidents, as well as verify compliance with contractual clauses related to the topic.
GRI 403
Occupational Health and Safety Management Programs
Copel’s programs of management in health and safety at work aim at keeping the work environment safer, preventing accidents and occupational diseases by means of the identification of possible risks, analysis of the environment where they manifest themselves and the creation of action plans for prevention, mitigation or elimination of these risks. For this purpose, Copel maintains the Health and Safety Management System, highlighting the Risk Management Programs (PGR) and the Medical Control of Occupational Health Program (PCMSO), which are feedbacked and consider aspects related to the different regulatory standards, activities, hazards and environmental risks for each job, function or activity developed in the company’s units, focusing on the identification of possible injuries and aggravations caused by these risks and, consequently, affecting the workers’ health and safety.
Risk Management Program
The Risk Management Program (PGR) aims to manage risks, evaluate processes, and propose, by means of an action plan, solutions to prevent accidents that might put the worker’s safety and physical integrity at risk, avoid occupational risks that might originate at work; identify the dangers and possible injuries or health hazards; evaluate the occupational risks, indicating the risk level; classify the occupational risks to determine the need to adopt prevention measures; implement prevention measures, according to the risk classification; monitor the control of occupational risks.
The mapping of hazards and risks is carried out by means of the Risk Inventory, which makes up the PGR – Risk Management Program, using the criteria of severity, probability, employee exposure, effectiveness of existing controls, and concentration. The Risk is graded as:
- Negligible (Insignificant): at this level it is not necessary to implement new controls.
- Acceptable (Insignificant): at this level it is not necessary to implement new controls, it is recommended to evaluate the possibility of implementing more controls in order to reach the Negligible level.
- Moderate (Significant): at this level it is important to implement controls to reduce the risks, aiming at least at the Negligible or Acceptable level.
- Substantial (Significant): at this level, controls must be implemented to reduce risks, aiming at the Acceptable level.
- Unacceptable (Significant): at this level, the activity cannot be performed until controls are implemented, reaching at least the Substantial level, and then new measures must be implemented seeking to reach the Despicable or Acceptable level.
The process is conducted by the safety area in conjunction with the employees and/or CIPA. All professionals in the safety area are technically qualified for hazard and risk analysis and instruct employees in the methodology before the assessment process begins.
The measures proposed to minimize the hazards and risks are inserted in the Action Plan, which is also part of the Risk Management Program, and are followed up in the Critical Analysis Meetings, which occur periodically.
For the prioritization and integration of the action plans, the risks are assessed, following the methodology of probability versus severity and exposure, through the risk inventory (one of the items that make up the RMP). According to the results, action plans are created, prioritizing the risks with the highest scores. This way, the risks are mitigated, which impacts on the reduction of work accidents and the consequent reduction of the values of the indicators related to this theme.
Occupational Health Medical Control Program
The Occupational Health Medical Control Program (PCMSO) has as its main objectives: the promotion and preservation of the health of all the company’s employees, seeking to prevent, track and early diagnose changes in health status, mainly arising from the nature of work, as well as how to determine the employee’s physical and mental fitness conditions for the safe exercise of their duties, track situations that may have an impact on the employee’s working capacity and quality of life in the future, in addition to establishing the mandatory and periodicity of medical evaluations, complementary exams and medical-administrative conduct to be taken.
The PCMSO is connected to the Risk Management Program (PGR) and considers aspects related to different regulatory standards, activities, dangers and environmental risks for each position, function or activity, with a focus on identifying possible injuries and injuries caused by these risks .
One of the focuses of occupational health is the monitoring of problems to workers’ health, which can lead to occupational illnesses. To this end, a surveillance and investigation process is used with multiple inputs, from periodic medical examinations to monitoring absences/absenteeism, special assessment for behavioral and productivity changes and also direct requests for restrictions or absences.
Once a disease whose cause may be related to the work activities carried out has been identified, after the initial investigation stage with complementary exams and specialized medical evaluation, such data is associated with social and ergonomic evaluation, whenever necessary, confirming (or ruling out) the causal link for the employee and ensuring that such risk factors are resolved for the safe return to work and even for other colleagues in similar conditions, in addition to the correct registration of the case, guaranteeing all the worker’s rights.
Progress in disease prevention and health risk reduction is assessed monthly by a multidisciplinary team, aligning these factors with organizational results and targets.
Risk Hunting Program
The Health and Safety Portal (PSS) allows you to record and consult “Risk Hunting” and “Near Miss” events. The environment allows you to report in detail the situations you have witnessed, indicating the location and, if you prefer, suggesting actions to resolve the risk. The record can also be made anonymously. It is also possible to record CIPA minutes in the app, consult forms and regulations, sector scores and meeting calendars.
The Risk Hunting Program is a Copel initiative that seeks to involve workers in identifying potential risks of accidents in the company’s internal and external environments, with the aim of assisting the areas and entities involved in workplace safety, responsible for planning, executing , monitoring and managing the costs of preventive actions.
To optimize the recording and monitoring of this information, the initiative uses specialized program that allows consultation and active participation of workers, facilitating communication and sharing of data on identified risks. Furthermore, the system supports the planning and execution of security measures, ensuring that all actions are documented and accessible for analysis and review.
The management of identified risks is carried out by representatives of the Internal Accident and Harassment Prevention Committee (CIPA), who develop action plans focused on mitigating and eliminating risks. These plans are integrated into the system, allowing efficient monitoring and assessment of the impact of the measures adopted.
Internal Commission for Accident Prevention and Harassment
The Internal Commission for the Prevention of Accidents and Sexual Harassment (CIPA), altered by MTP Ordinance No. 4,219 of December 20, 2022, is composed of representatives of the employer and employees, with the objective of promoting the prevention of accidents and work-related illnesses, in order to contribute to a safe and healthy work environment, focused on the preservation of life, the promotion of worker health, and the fight against sexual harassment and other forms of violence at work. This is a requirement of the Brazilian legislation, foreseen in Federal Law 13.174/2001.
Prioritization and Action Plans
The company has an internal regulation that deals with prioritization and action plans on occupational health and safety.
This standard establishes rules for Occupational Health and Safety in order to prevent accidents and guarantee the integrity of the workforce within the scope of Companhia Paranaense de Energia – Copel (Holding) and its wholly-owned subsidiaries – SIs (direct and indirect), respecting their corporate procedures, and defines technical procedures aimed at eliminating or controlling the factors that can lead to the occurrence of incidents, accidents and/or occupational illnesses by identifying critical activities, hazards, risks and ways of blocking them.
All work must be carried out safely through planning, organization and training, the use of appropriate equipment, the use of suitable and up-to-date working methods, competent supervision, awareness, commitment and correct attitudes on the part of the workforce.
All activities will only begin when occupational health and safety conditions are met, and the workforce is guaranteed the right to postpone the activity.
The practice of occupational safety, health and quality of life must be disseminated as an essential activity for the entire workforce.
Hazards and risks must be identified on an ongoing basis through the Risk Management Program (RMP), which can be implemented by operational unit, sector or activity, containing at least a risk inventory and action plan.
In the case of contracting, contractors who have their own procedures may use them, provided they are approved by the occupational safety department.
The procedures must be disseminated to the workforce involved and be kept up to date and available in easily accessible media, making up, along with the other occupational health and safety instructions, the safety service orders provided for in NR01¹.
All employees must receive instructions on precautions to prevent accidents at work or occupational illnesses, in accordance with NR01¹.
Procedures must be monitored for compliance with occupational health and safety requirements.
The inspection must be recorded in a specific system, including proposals for mitigation actions, where appropriate. mitigation actions, where appropriate.
¹ NR01 stands for Regulatory Standard 01 and is a safety standard issued by the Brazilian government through the Ministry of Labor and Employment.
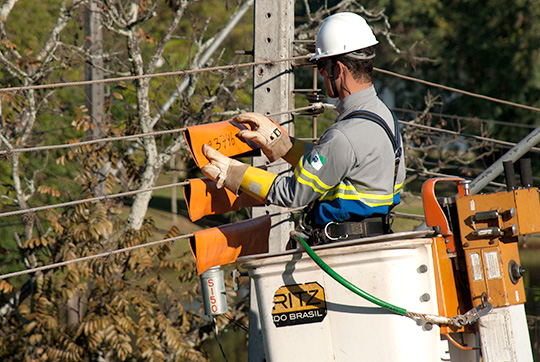
Actions from Copel Distribuição
As a way of ratifying the importance of occupational health and safety at Copel Distribuição, the consolidation of the culture of safety, health and quality of life must be aligned with the Company’s values and the expectations of the stakeholders.
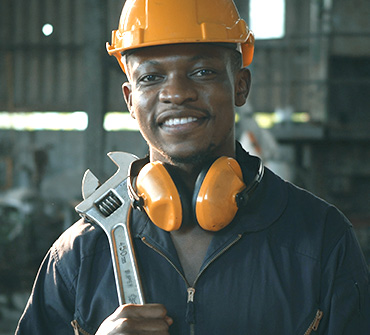
Actions from Copel Geração e Transmissão
Guided by the occupational health and safety policy, Copel Geração e Transmissão (Copel GeT) has as a guideline that everyone is responsible for safety and understands that all accidents can be avoided.
Accident Data
Consolidated
Companhia Paranaense de Energia
Lost-Time Injury Frequency Rate (LTIFR)
TFLA | 2019 | 2020 | 2021 | 2022 | 2023 | 2024 |
Employees | 2.36 | 2.19 | 1.85 | 1.84 | 5.99 | 1.95 |
Coverage | 100% | 100% | 100% | 100% | 100% | 100% |
Contractors | 5.27 | 7.35 | 7.38 | 6.59 | 15.59 | 4.01 |
Coverage | 100% | 100% | 100% | 100% | 100% | 100% |
The indexes were calculated for every 1,000,000 hours worked, and no worker was excluded from the calculation. |
Fatalities
Fatalities | 2019 | 2020 | 2021 | 2022 | 2023 | 2024 |
Employees | 0 | 0 | 0 | 0 | 1 | 0 |
Contractors | 1 | 5 | 2 | 3 | 4 | 1 |
By Company
Methodology: NBR 14.280, Regulatory Standard for Work Accident Registration issued by the Brazilian government through the Ministry of Labor and Employment.
Compania Paranaense de Energia
Year | Employee type | FR | GR | Number of deaths |
2018 | Own | 4.11 | 148 | 0 |
2018 | Hired | 6.42 | 890 | 2 |
2019 | Own | 2.36 | 84 | 0 |
2019 | Hired | 5.27 | 558 | 1 |
2020 | Own | 1.12 | 66 | 0 |
2020 | Hired | 5.81 | 1,953 | 5 |
2021 | Own | 1.01 | 50 | 0 |
2021 | Hired | 5.85 | 926 | 2 |
2022 | Own | 1.09 | 17.79 | 0 |
2022 | Hired | 5.65 | 19,442.13 | 3 |
2023 | Own | 1.34 | 624.56 | 1 |
2023 | Hired | 64.70 | 19,088.29 | 4 |
2024 | Own | 2.04 | 56.69 | 0 |
2024 | Hired | 3.95 | 410.56 | 1 |
FR – Frequency Rate
GR – Severity Rate
Copel Comercialização
Year | Employee type | FR | GR | Number of deaths |
2018 | Own | 0 | 0 | 0 |
2018 | Hired | 0 | 0 | 0 |
2019 | Own | 0 | 0 | 0 |
2019 | Hired | 0 | 0 | 0 |
2020 | Own | 0 | 0 | 0 |
2020 | Hired | 0 | 0 | 0 |
2021 | Own | 0 | 0 | 0 |
2021 | Hired | 0 | 0 | 0 |
2022 | Own | 0 | 0 | 0 |
2022 | Hired | 0 | 0 | 0 |
2023 | Own | 0 | 0 | 0 |
2023 | Hired | 0 | 0 | 0 |
2024 | Own | 12.29 | 12.29 | 0 |
2024 | Hired | 0 | 0 | 0 |
Copel Distribuição
Year | Employee type | FR | GR | Number of deaths |
2018 | Own | 5.75 | 133 | 0 |
2018 | Hired | 7.83 | 1,169 | 1 |
2019 | Own | 2.87 | 114 | 0 |
2019 | Hired | 5.59 | 197 | 0 |
2020 | Own | 1.66 | 131 | 0 |
2020 | Hired | 5.06 | 2.017 | 4 |
2021 | Own | 1.71 | 74 | 0 |
2021 | Hired | 4.88 | 935 | 2 |
2022 | Own | 1.14 | 17 | 0 |
2022 | Hired | 5.87 | 1,479 | 2 |
2023 | Own | 1.31 | 883.45 | 1 |
2023 | Hired | 66.80 | 21,439.75 | 4 |
2024 | Own | 1.65 | 64.51 | 0 |
2024 | Hired | 4.20 | 483.57 | 1 |
Copel Geração e Transmissão
Year | Employee type | FR | GR | Number of deaths |
2018 | Own | 2.66 | 32.26 | 0 |
2018 | Hired | 4.14 | 1,868.13 | 1 |
2019 | Own | 1.24 | 9.06 | 0 |
2019 | Hired | 4.59 | 1,809.06 | 1 |
2020 | Own | 0.87 | 2.18 | 0 |
2020 | Hired | 9.25 | 2,058.63 | 1 |
2021 | Own | 0.45 | 0.90 | 0 |
2021 | Hired | 10.99 | 98.89 | 0 |
2022 | Own | 1.48 | 2.18 | 0 |
2022 | Hired | 11.53 | 250.68 | 0 |
2023 | Own | 1.53 | 7.66 | 0 |
2023 | Hired | 75.72 | 4.486.57 | 0 |
2024 | Own | 3.20 | 49.36 | 0 |
2024 | Hired | 4.0 | 16.02 | 0 |
Copel Holding
Year | Employee type | FR | GR | Number of deaths |
2018 | Own | 0 | 0 | 0 |
2018 | Hired | 2.60 | 78 | 0 |
2019 | Own | 0 | 0 | 0 |
2019 | Hired | 1.33 | 40 | 0 |
2020 | Own | 0 | 0 | 0 |
2020 | Hired | 0 | 0 | 0 |
2021 | Own | 0 | 0 | 0 |
2021 | Hired | 0 | 0 | 0 |
2022 | Own | 0 | 0 | 0 |
2022 | Hired | 0 | 0 | 0 |
2023 | Own | 0 | 0 | 0 |
2023 | Hired | 13,47 | 40.41 | 0 |
2024 | Own | 0 | 0 | 0 |
2024 | Hired | 1.30 | 33.05 | 0 |
FR – Frequency Rate GR – Severity Rate