Copel Generation and Transmission Shares
Guided by the Occupational Health and Safety policy, Copel Geração e Transmissão (Copel GeT) has as a guideline that everyone is responsible for safety and understanding that all accidents can be avoided.
Several actions are developed throughout the year always guided by the risks raised. Among these actions we highlight:
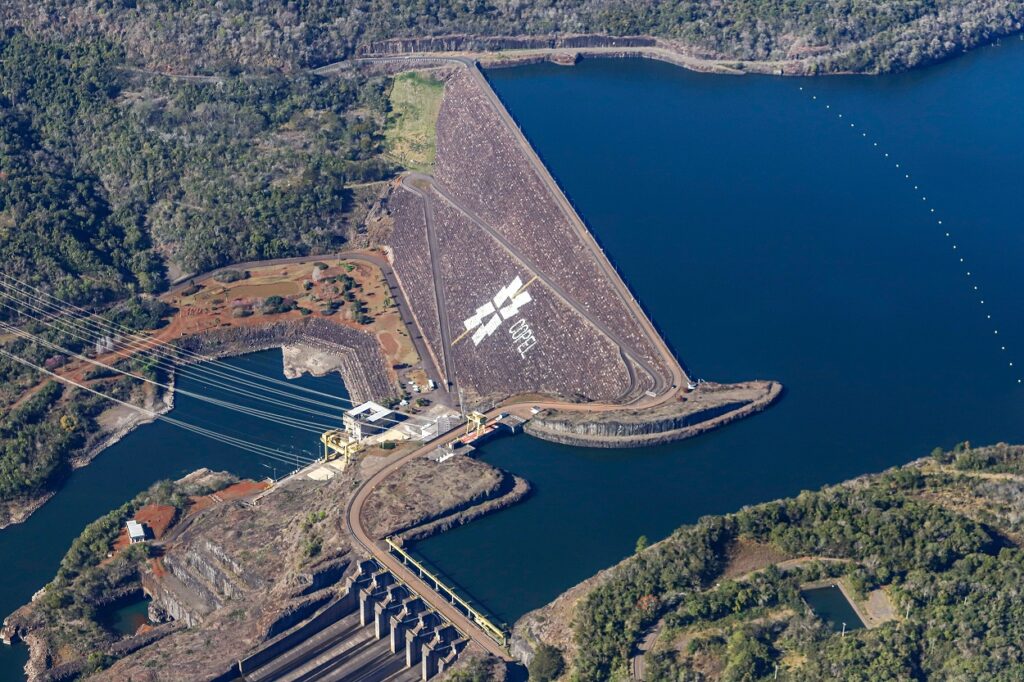
Initially launched as a campaign, focused on encouraging safe behavior, based on accident statistics and on the concept of Active Care, it later evolved into a permanent program with several integrated actions. From the beginning, the premise of co-responsibility was widespread and internalized. Over the years, several classes have completed the Behavioral Safety Training Course, with professionals from different areas of Copel GeT, where a change in the way the employees’ behavioral approach was started, counting on different actions of the program (Wworkshops, Ccampaigns, SIPATs, Ppalestras, videos, promotional materials, e-mails, procedures, besides several Communication actions) that sought to highlight and value actions that focused on Behavioral Safety.
Behavioral Check – VCO
VCO is a method of observation and interaction with the workforce, focusing on people’s attitude and behavior while carrying out their activities, in real time. The method uses a technical approach, based on awareness and continuous improvement of performance in Safety, Health and Environment with main objectives:
- Contribute to the evolution of the safety culture;
- Improve risk perception;
- Disseminate the culture of active care;
- Contribute to the development of active safety indicators; and
- Direct actions and investments in Occupational Safety.
The system consists of filling out a form about security procedures and verification data launched directly into a mobile application, allowing real-time analysis which saves time, increases reliability, centralizes the management of recorded data, standardizes forms and security reports. occurrences and speeds up decision-making to correct any deviations identified in the areas, in addition to supporting the definition of priorities for managers’ actions in actions aimed at occupational health and safety.
The management of risks related to health and safety is carried out through an integrated approach that involves several programs and committees:
- Risk Management Programs (PGR) – structure the identification, assessment and control of occupational risks, following strict safety standards.
- Internal Accident and Harassment Prevention Committees (CIPA) – dedicated committees that work together with Emergency Brigades to respond to incidents and promote preventive practices.
- Behavioral Checks – observations and interactions focused on the attitude and behavior of employees, aiming to continuously improve safety.
- Safety Inspections – regular assessments of working conditions to identify and mitigate potential risks.
- Security Sector Meetings (RSS) – periodic meetings to discuss security issues and share best practices.
- Risk Hunting System – platform where employees can actively report identified risks, contributing to collective security.
These methods, together, form a robust safety network that allows not only the identification and treatment of risks, but also the active participation of employees in building a safer work environment.
It awards the best Safety Campaign, within the annual cycle, highlighting the actions carried out by the CIPAs and appreciating the dedication and commitment of the employees. The award is delivered by the General Director of Copel GET.
Developed in Copel GeT’s three largest plants, this project aims to diagnose the maturity level of the safety culture and to prepare a cultural transformation plan focused on the development of actions that will contribute to reducing work accidents and improving the maturity level in behavioral safety.
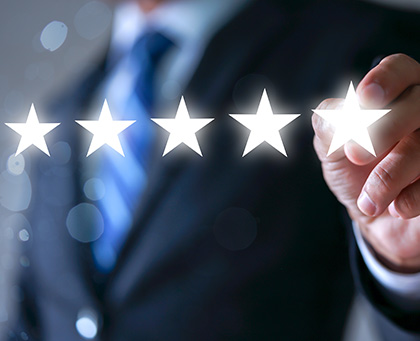
- Dealing with the risks identified by means of the Risk Management Programs - PGR, by the Internal Commissions for Accident Prevention - CIPA and Emergency Brigades, by Behavioral Checks and safety inspections, by Sectorial Safety Meetings - RSS, and also by the Risk Hunting System, where employees can report the risks they identify.
Integrated Management System
Copel Geração e Transmissão S.A. seeks excellence in specialized services for the operation and maintenance of power plants, with a commitment to:
- Preventing occupational injuries and diseases, mainly caused by traffic and electricity;
Adopt a preventive systemic approach in order to eliminate hazards and reduce risks, with the aim of preventing accidents and ensuring safe and healthy working conditions; - Promote consultation and encourage worker participation in forums and environments suitable for information and discussion of occupational health and safety issues;
- Protect the environment, through the prevention of pollution, especially that caused by industrial oils, the optimization of material, water and energy consumption, and the environmentally correct disposal of waste
Rationalize costs; - Optimize the indices of availability and reliability;
- Meet the relevant legal requirements and other applicable requirements; and
- Implement continuous improvement in the performance of quality, health and safety, and the environment, in alignment with corporate policies and guidelines.
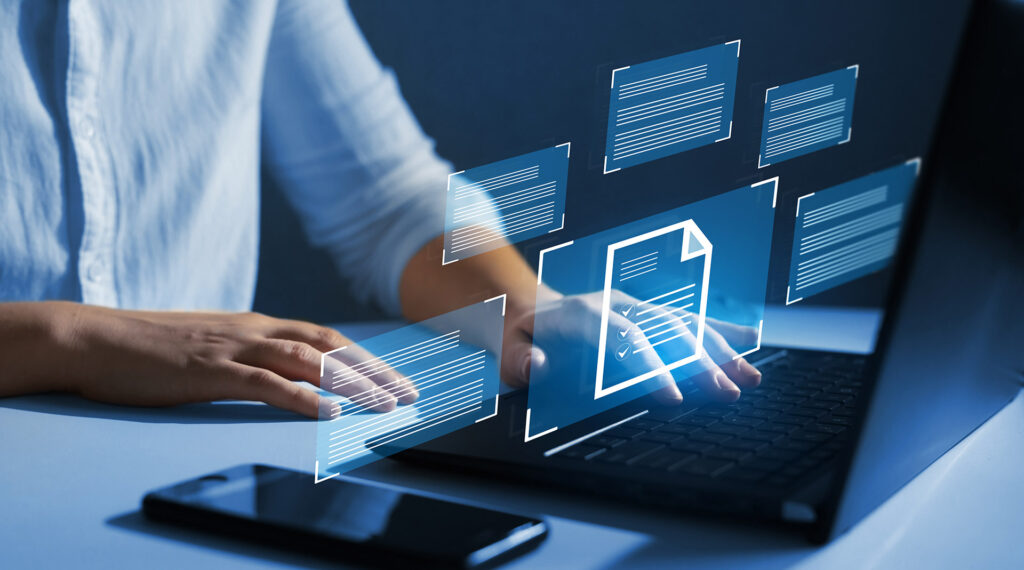
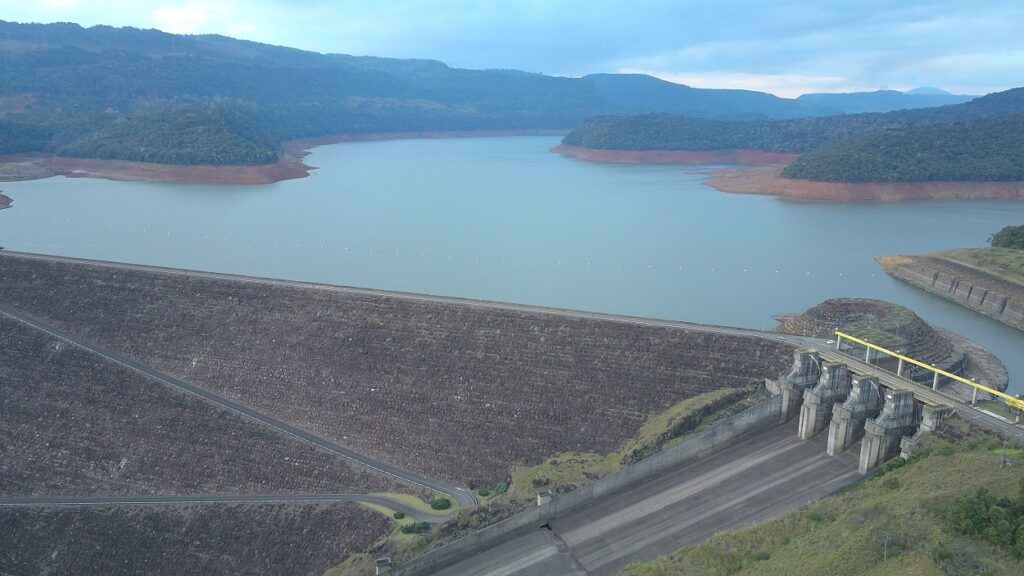
In the context of Occupational Safety, five of Copel GeT’s main plants are certified by standard 45001:2018 – Occupational Health and Safety Management Systems. This certification is an international recognition that attests to the company’s commitment to the safety and health of its employees, following strict occupational risk management standards.
The certified plants, according to the scope “Operation and maintenance processes of Energy Generation Infrastructure”, are:”
- UHE GBM – Gov. Bento Munhoz da Rocha Netto Hydroelectric Plant (Foz do Areia);
- UHE GNB – Gov. Ney Aminthas de Barros Braga Hydroelectric Plant (Secret);
- UHE GJR – Gov. José Richa Hydroelectric Plant (Salto Caxias);
- UHE DRJ – Jordan River Derivation Hydroelectric Plant; and
- UHE GPS – Governador Pedro Viriato Parigot de Souza Hydroelectric Plant.
These certifications reflect the high safety standards adopted by Copel GeT and its continuous commitment to improving working conditions and preventing accidents.